05 August 2021
Home-Building at Breaking Point
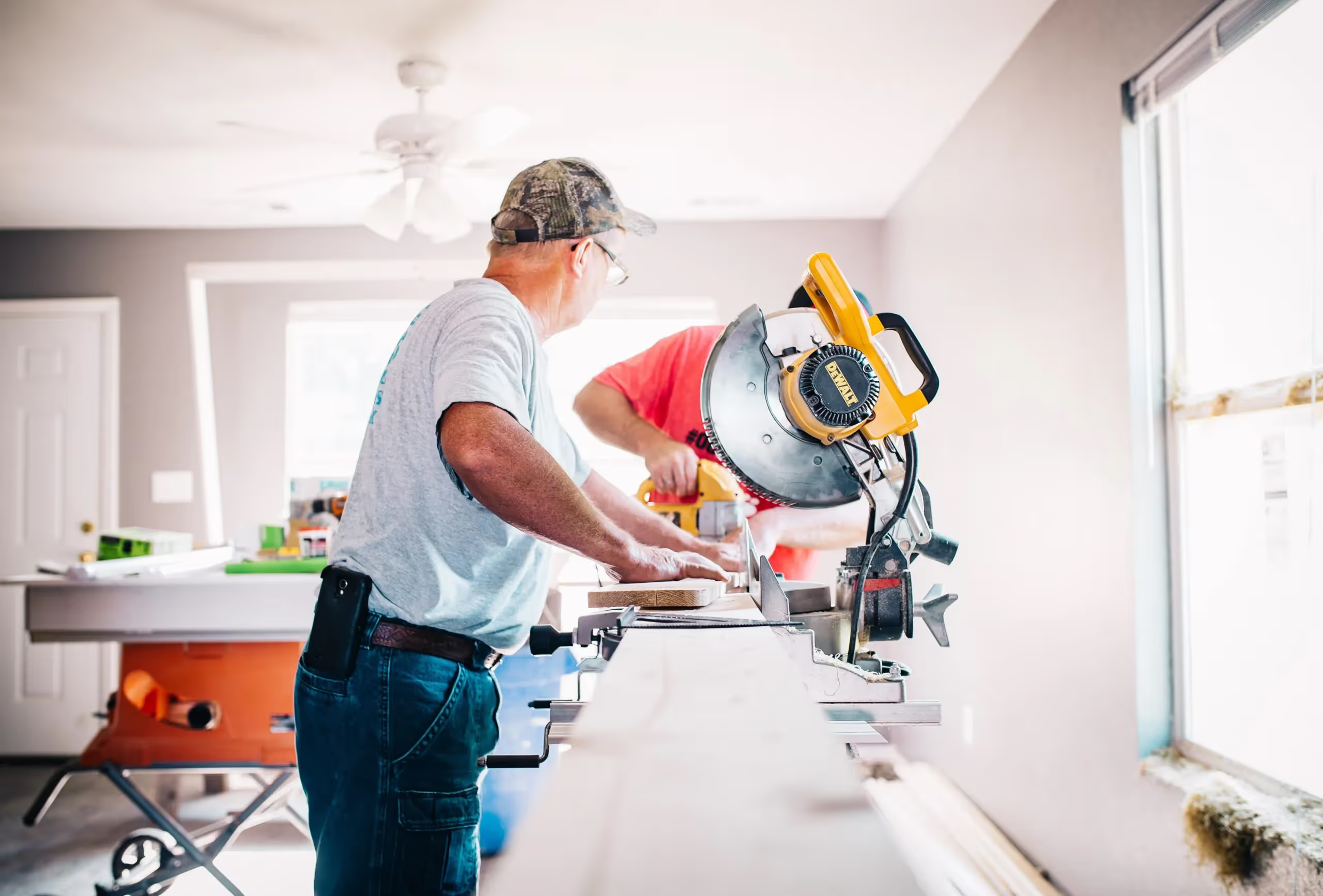
A construction supply crisis is affecting key development projects across the country as builders deal with a critical shortage of building materials. There is no doubt that a construction boom is playing out across the country. Home building is at six-year highs, with approvals for detached homes increasing 3.4 per cent to a seasonally-adjusted record of 15,160 in April. This boom has created major challenges in the supply chains with builders telling developers that projects can’t start on time, resulting in cost blowouts and half-built developments, particularly in the residential sector. Some suggest that a surge in building activity on the back of policy announcements to stimulate the economy forced developers to act swiftly. But, they say, these announcements came without proper forethought about the implications and consequences, leading to the current construction supply shortages. However, a range of other factors have played a role in the shortage, including rising shipping costs due to a shortage of empty containers because of Covid-19, rising labour costs, record low-interest rates and a national housing shortage, building materials defects, and unprecedented demand for new housing stock across the country. The shortage is leading to construction delays and also builders being forced to turn away paying clients—and there is no end to the materials shortage in sight. A number of building supplies are in short supply, with timber and steel topping the list.
Difficult times ahead
One house builder has taken the extraordinary step of contacting its clients to outline the full extent of the crisis. In a three-page letter shown to The Urban Developer, clients were told the broader industry was facing challenging times. “The following information is not intended to be an excuse for difficult times, it is just the facts that are facing the construction industry,” it read. “We are working tirelessly to find ways to work through all of our internal and external issues and hope for your support and understanding in these unprecedented times.” The letter goes on to explain that housing starts have increased dramatically on the back of stimulus packages, which is driving up the price of building materials, many of which are now traded on global markets. “Australia, like all countries, is having to compete for these materials and pay the global market price.”
It also explains that structural pine, used for house framing, is in short supply. The issue was worsened by the 2019-2020 bushfires, which wiped out significant Australian pine forests. This has driven up competition for limited supply, which is being passed on to all parties in the supply chain, affecting the cost of building here in Australia and the ability to source products in a timely manner. Disruption in supply chains to raw materials and finished goods have also interrupted supply of goods and construction progress. Similar construction supply shortages are being reported across the United States and the United Kingdom, where shortages extend to other building materials including cement and paint. The bottom line for developers is that the cost of builds could increase in the coming year or two as builders are urged to account for cost blow-outs in their contracts.
Frustration amid delays
Carnelian Projects director Kerri-Ann Hooper started noticing supply issues in February. “There are frustrated clients who just want their build to start, and then there are builders who cannot get trades or supplies and are just throwing their hands in the air in frustration,” she said. “What is happening at the moment effects concreters, timber frames, even some glue supplies—it is just crazy. “And this perfect storm has impacted land and house prices, which in turn affects people’s borrowing capacity.” Desperate builders are taking insurance jobs over new builders to shore up their income, while some major builders are paying big money to secure builders, she revealed.
Meanwhile, price blowouts are appearing. Trusses and frames have doubled in price as supply and demand impacts pricing, she said. It’s a national problem. In south-east Queensland, the owner and CEO of 4Shore Projects, Joe Dageforde said that developments were being hampered by a lack of materials, particularly steel from China. Backordered building materials are holding up projects for months, he said. Sydney’s Andrew Jhavery of Ark Joinery said many of his long-standing suppliers are at record lead times, some in excess of six months from ordering times. This compared to next day delivery before Covid-19. “Massive demand as well as with unprecedented times (due to Covid-19) mean that our high reliance on overseas-manufactured commodity product to fuel our industry is going to hit hard in the coming months when stock is not actually available,” he said.
Supply and demand has always played an important role in maintaining a strong economy, Stallion Property Group director Stephen Cromie said. “Someone once told me that the strength of the NSW economy can be seen by how many cranes are up, and that is so true,” Cromie said. “But items such as frames and trusses have blown out from a usual lead time of six weeks out to 10 weeks. “At Bunnings, you can’t buy timber over 4.8, in 90x45mm. Carpenters are turning away work because they simply can’t get the materials, and because of this demand, prices have gone up. “All this will result in further housing shortages, which will keep homes from becoming affordable any time soon.”
Cost blowouts
In Melbourne, the managing director of ID_Land Matthew Belford revealed it was a constant case of over-promise and under-deliver across the supply chain. “We have suppliers of frames, for example, who ring us up and say ‘we think we’re getting 30 pallets of frames next week’ and then they ring us back a week later and say only 10 had arrived,” he said. “We are losing time, and if ever I’ve learned something from business it’s that time is a killer—it’s what erodes margins in businesses over time. Belford said they were looking at ways to shore up supply including replacing timber with steel. “You’ve just got to adapt, but it’s a genuine pressure. We’ve got dated contracts. All that’s going to happen over time is some margin erosion,” he said. “We talk to the major timber suppliers … and when they say ‘we’ve never seen anything like this before and we don’t know when it’s going to stop’ it doesn’t give you much hope. “Most people have a view that it’s a six to 12-month timeframe, but the problem is we’ve still got the demand piling in.”
Contracts may change
The Association of Professional Builders co-founder Russ Stephens said that builders were feeling duped by suppliers they had supported through challenging times, which had not been reciprocated, leaving them in the lurch. “The latest boom has spurred hundreds of additional projects and some builders feel their suppliers are taking unfair advantage of the situation,” Stephens said. “When supplies are low, charges inevitably go up, but not everyone feels the higher price tags are reasonable. “As a result, costs are exceeding budgets by thousands of dollars. “Meanwhile, a lack of availability is causing huge delays, meaning builders are struggling to stay on schedule. “In most cases, the builder will have to bear the additional cost, eroding any net profit left in the project.” No business should be forced to press on with starting a project knowing they will be running at a loss, he said.
The association has urged builders to be cautious when signing fixed price contracts due to cost blowouts, and to consider inserting cost escalation clauses that will protect their businesses from the rapid inflation being experienced. The issue is affecting program considerations and developer confidence, Mitchell Brandtman partner Matt Hemming said. “The cost to lay a brick is more expensive than it was years ago due to opportunistic pricing,” he said. “Really, it becomes a case of exploring what the contractual rights are.” Looking at the big picture, the cost of developing will rise, according to one independent economist. BIS Oxford Economics associate director Adrian Hart said that upward pressure on construction costs would emerge from 2022-2023 as the dollar of work done rises to levels that had not been seen before. “It hasn’t hit us yet, but as we go forward during the next few years, I anticipate that we might start to see a pickup in some of these prices,” he said in a recent online conference. The team at Windsor Capital Management are here to help and are more than happy to answer any questions you may have.
To find out more visit our website www.windsorcapital.com.au
Insights
More News
Contact Us
Want to
know more?
Talk to our investor relations team today to see if Windsor Capital could fit your investment strategy and portfolio.
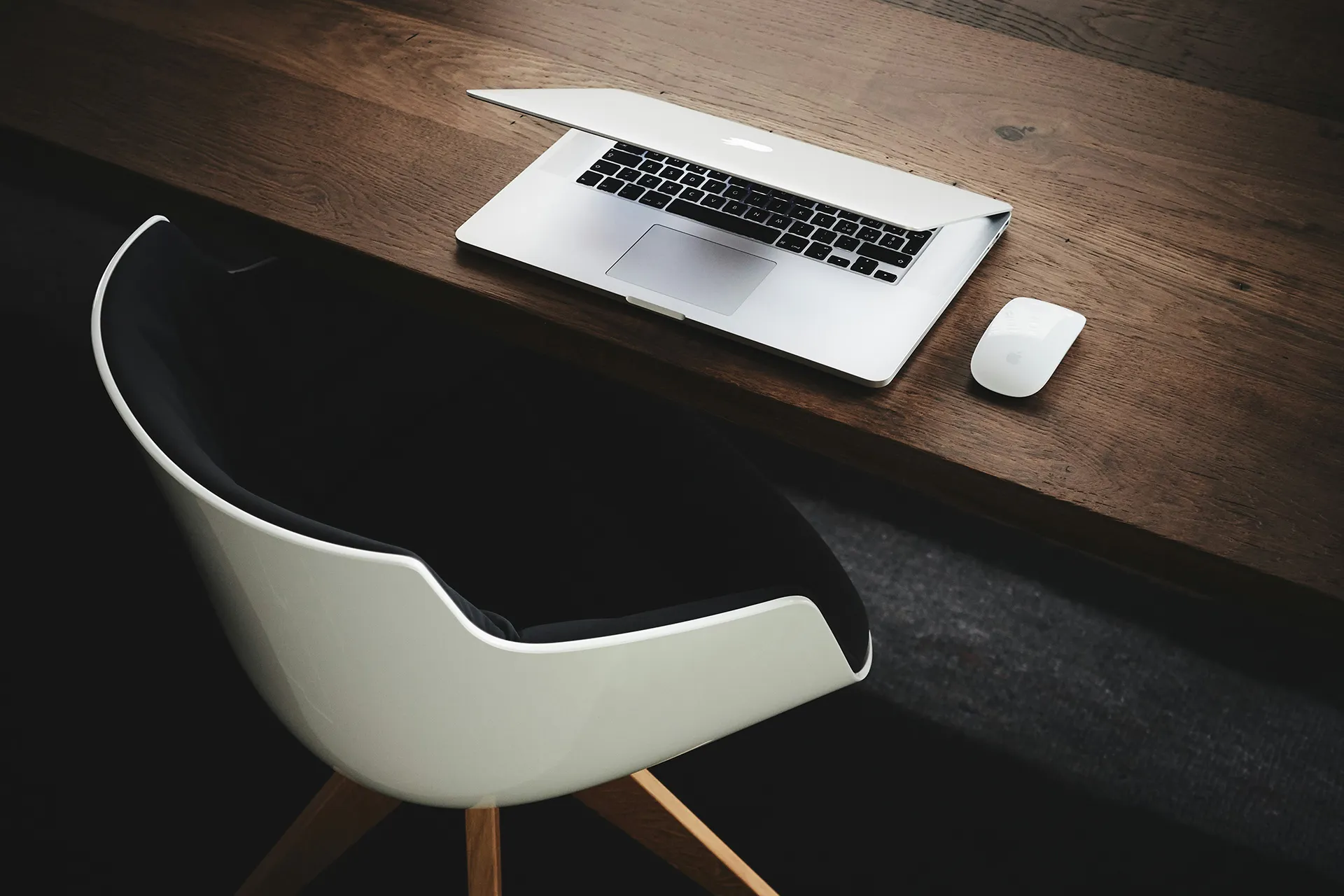